At present, information technology with computer technology as its core is being widely used in manufacturing industry, and information technology has become one of the key development directions of manufacturing technology. The key to informatization lies in data. Informatization without data is just an empty shelf. The process data generated by CAPP is not only an important part of product data, but also the “blood†of normal operation of enterprise PDM, ERP and so on. Therefore, the implementation of CAPP will be a watershed for the success of enterprise information construction. In-depth research on the tracking and implementation of CAPP technology level is of great significance and far-reaching impact on modern manufacturing enterprises.
1. Manufacturing Enterprise Integration and CAPP System
The Modern Integrated Manufacturing System (CIMS) combines information technology, management technology and manufacturing technology and applies it to all phases of the enterprise product life cycle. Through the sharing and integration of information, the optimization of processes and resources, the integration and optimization of material flow, information flow, value flow and knowledge flow are realized, thereby improving work efficiency and design level, and ultimately improving the market resilience and core competitiveness of enterprises. .
Manufacturing enterprise integration is realized by computer network technology, database technology and system technology, and realizes data sharing and process integration from design, management, to manufacturing. Figure 1 is the structural framework of manufacturing enterprise integration. Obviously, CAD is only responsible for turning design ideas into drawings, and the production process is a collection of discrete events. They are not able to achieve enterprise-level integration, nor can they provide macro guidance for corporate decision-making. CAPP solves the problems of acquisition, processing, management and accumulation of process data through product data sharing and system coordination, achieving rapid mobilization, optimization and integration, efficient use of enterprise resources, and support for enterprise decision-making. It can be seen that the CAPP system is a bridge from design to manufacturing, a collection of product information, and a truly decisive key technical link to achieve manufacturing enterprise integration.
2. System design requirements
2.1 Product-oriented life cycle
In the era of knowledge economy, manufacturing products are developing in the direction of individualization, multi-variety and volume change. Enterprises must comprehensively consider the TQCSE of products, and even include cultural and social effects. If the CAPP system still stays in the function of turning the drawings into physical objects, it is far from meeting the needs of modern manufacturing companies for CAPP. As the hub of corporate activities, CAPP should participate in the whole process of enterprise analysis from market analysis to after-sales service (as shown in Figure 1). From the whole life cycle of the product, it can quickly provide process data, efficiently reuse knowledge, and obtain relevant information in time. Optimize design results and participate in various activities throughout the process to achieve design and management of large process flows. This requires the CAPP system to consider the manufacturability, assemblability and maintainability of the design, the feasibility and verifiability of the process, the cost and benefit of the production, the product schedule and function, etc. during the engineering design phase. The full life cycle performance is evaluated by the process.
Figure 1. Manufacturing enterprise integration structure framework
2.2 Support for concurrent engineering
Concurrent engineering emphasizes that all activities of the enterprise should start as soon as possible and strive for a success; emphasize the inter-system interconnection, mutual support and mutual restraint; emphasize the effective optimization and cooperation to achieve overall optimization and improve the flexibility and competitiveness of the whole system. First of all, the process design is multi-tasking and multi-role. CAPP itself must be a platform for parallel work, coordination and information sharing. Secondly, CAPP should consider the functional requirements of parts, manufacturing capabilities, environmental testing, quality inspection, production costs, equipment load and planning progress, etc., which is the center of functional coordination among various systems. The process evaluation of achieving the full life cycle performance of the product is the goal and key of the CAPP system to support concurrent engineering.
2.3 Implementing enterprise integration
Introduce PLM, WEB and database technology into CAPP system, establish a multi-layer distributed architecture, realize data parallel transmission and automatic information exchange between CAPP system and other systems, realize knowledge sharing and reuse and information enterprise integrated. Integration is a multi-level, phased, and gradual process. The key is to ensure that enterprise information is transmitted, exchanged, and exchanged in an orderly, controllable, secure, and convenient manner among systems. Realizing enterprise integration is the technical implementation path of CAPP for product life cycle and supporting concurrent engineering.
Next page
Yupdeng LED Module-Slim
Product categories of Led module-slim, we are specialized manufacturers from China, led module flood light suppliers/factory, wholesale high-quality products of waterproof led modules R & D and manufacturing, we have the perfect after-sales service and technical support. Look forward to your cooperation!
Company
Founded in 2004, Jiangmen YIDENG Lighting Technology CO., LTD has evolved into a global company that designs, engineers and manufactures innovative and decorative lighting solutions with a new sustainable LED collection for residential, retail, hospitality, museum, industrial and commercial applications.
We have developed an extensive line of award-winning LED luminaires including patented products and revolutionary LED fixtures. Technical innovation is central to what people have come to expect from YIDENG Lighting brand.
YIDENG Lighting has become a recognizable brand name as the microwave sensor leader with a stellar reputation for excellence in technology and design: a reliable name that you can trust for superior quality, innovative technology and superlatives service.
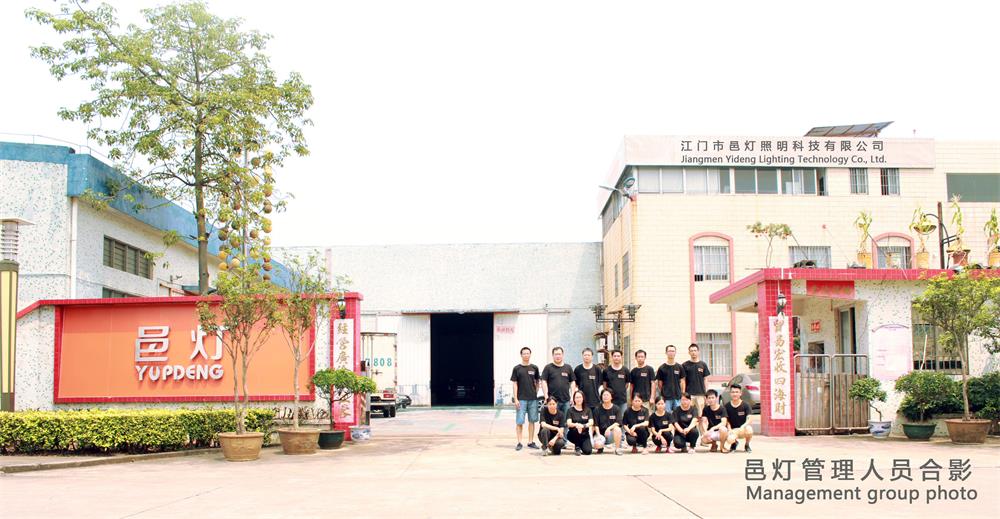
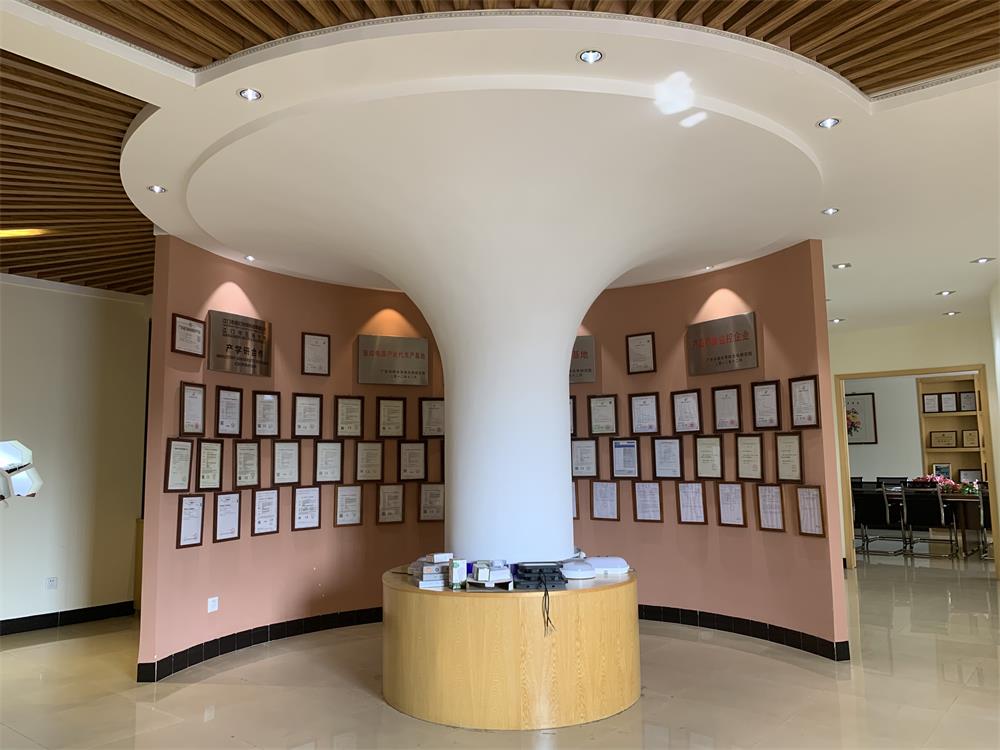
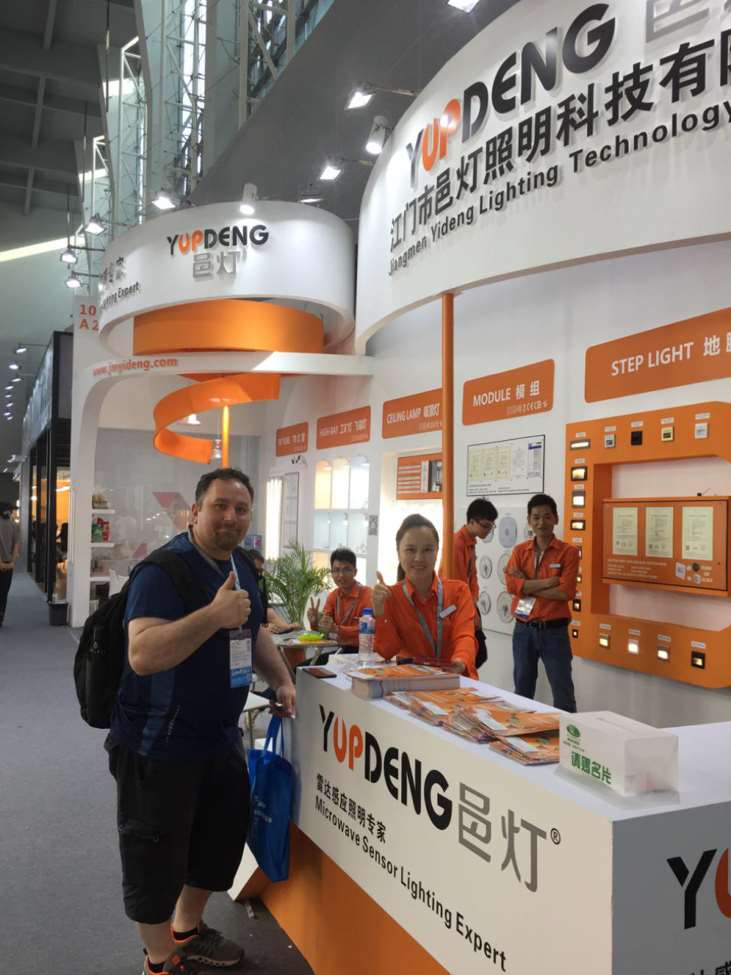
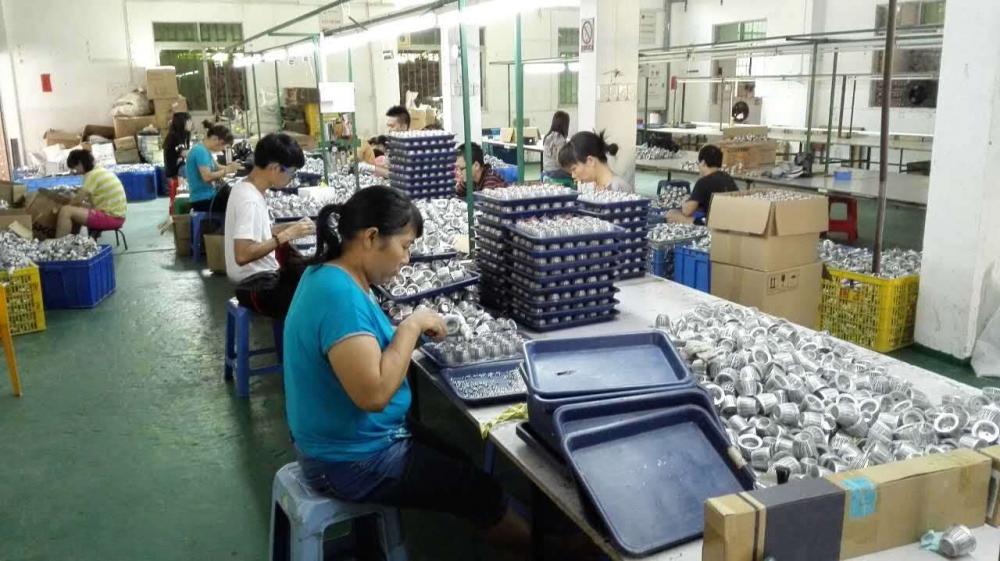
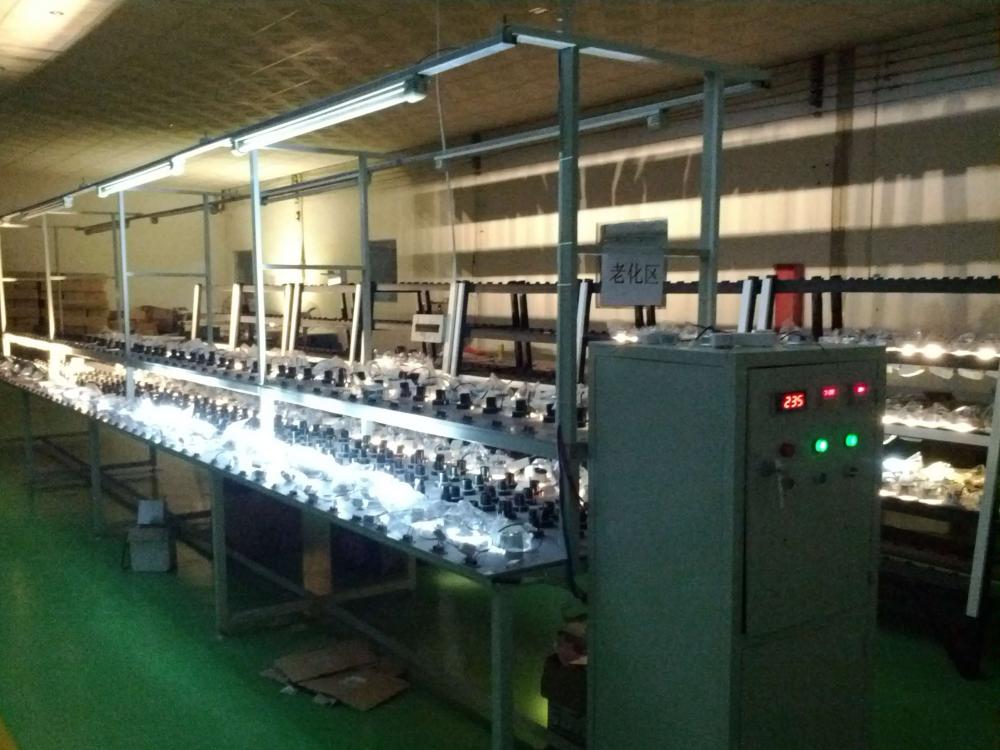
- Please click on the pictures and words for details.
- Except LED Spotlight ,we are also professional on indoor and outdoor lighting product for projects.
- Such as:LED Down Light, LED Track Light, LED Ceiling Light, LED Ceiling Light Module, LED Bulb, LED Step Light and other small lighting products as so on .
- We are not only a manufacturer, but also your expert lighting solution provider.Anything you ask, we will try our best to meet your requirements.
Led Module Flood Light,Waterproof Led Modules,Led Module For Ceiling Light,Ceiling Light Led Module
Jiangmen Yideng Lighting Technology Co,.Ltd , https://www.jmyideng.com