In the modern machine tool industry, machine noise has become one of the important indicators for evaluating the performance of machine tools, and the national standard ((GB/T16769—1997 Noise Measurement Method for Noise of Metal-cutting Machine Tools)†has also made mandatory provisions on this, and the whole machine tool has been The noise level of the machine noise should not exceed 83dB(A).In general, the noise of the spindle box (main drive) is the highest in the noise of the CNC machine tool, because the high-torque arc tooth synchronous belt drive has an accurate transmission ratio. With the advantages of high efficiency, high power, smooth transmission, and easy maintenance, the main drives of modern CNC machine tools increasingly employ high-torque arc synchronous belt drives.Therefore, how to control synchronous belt drives at high speed Noise has become an important issue in controlling headstock and even machine noise, and after a series of studies and experiments, a set of effective measures has been summarized to significantly reduce the noise of the machine belt.
Controlling noise mainly starts from two aspects: First, think of methods from sound sources, that is, eliminate or reduce the intensity of sound sources. This is the fundamental method to control noise, and is the focus of this article; the second is to absorb the noise from the transmission route. Sound, sound insulation and other measures to weaken or shield the spread of noise. There are two main reasons for analyzing the noise source of the timing belt drive: on the one hand, due to the excitation of the unbalanced centrifugal force when the two pulleys are rotating, and on the other hand, the disturbance of the gas is caused when the belt and the pulley are meshed. Aerodynamic noise is generated. The main factors that cause noise in these two areas are listed below.
1. Main factors causing rotation imbalance (1) The shape tolerance and position tolerance of the pulley itself, including the tooth-tooth tolerance, tooth thickness tolerance and axial and radial runout of the pulley. The higher the manufacturing precision of the belt and the pulley, the smaller the impact at the time of meshing, and the higher the accuracy of the timing belt transmission, the lower the noise must be. Since both the timing belt and the pulley are manufactured by professional manufacturers, the accuracy of manufacturing can be effectively controlled, which will not be described here.
Parallelism of the two pulley shafts: Under normal circumstances, as the error of parallelism increases, the sound pressure level gradually increases. Therefore, the parallelism of the installation must be ensured when the spindle axis and the motor axis are installed. The parallelism of the two axes must be limited to (0.003 - 0.005)c (c is the center distance of the two pulley shafts).
(2) Rotation accuracy of the two pulley shafts Since both pulleys need to be rotated at a high speed and the rotation speed is higher than 6000 r/min, the unbalanced centrifugal force at the time of high speed rotation will cause tremor of the spindle and the motor shaft if no dynamic balance is performed. This in turn stimulates strong noise. For most manufacturers, only the spindle (including the pulley) has been dynamically balanced during manufacture and assembly. The motor shaft must also be balanced dynamically. The pulley is mounted on the motor shaft and the entire rotary axis is measured using a line dynamic balancer. The test was conducted and the material balance method was used to perform dynamic balancing (drilling on the pulley) to require the final dynamic balance accuracy level to reach G2.5. After this treatment, the vibration and noise of the drive can be reduced to different extents, and it is also very beneficial to increase the service life of the timing belt and the main shaft.
(3) The pre-tensioning force of the timing belt is different from that of the flat belt and the v-belt. The timing belt relies on meshing to transmit power, so it does not require much pre-tension. Excessive tension will seriously affect the service life of the belt. Serious noise. Under the effect of starting and impact torque, too small tension may cause the timing belt to skip and cause root fracture. How to choose the proper tension The more accurate method is to use the ultrasonic tension tester. If there is no tester, a simple set of tooling can also be made and measured as follows: As shown in Figure 1, one side of the timing belt is close to two belts. At the center of the wheel, a test force is applied, and the belt is bent inward to produce a deformation d. If d=S/64 (s is the single measurement length of the belt, unit: mm), the tension of the belt is considered to be appropriate. . Otherwise, the belt tension measurement diagram of Figure 1 adjusts the tension of the belt until it is suitable. The values ​​vary depending on the type and bandwidth of the tape. Specific information can be found. For example, for 40mm wide 8YU (8M) timing belts, d takes 39N. Experiments have shown that proper tensioning of belts can significantly reduce high-frequency noise, which is often referred to as "whistling sound."
Pulley tension measurement diagram 2. Control of aerodynamic noise In the case of high-speed rotation of the pulley, the high frequency of the meshing teeth of the belt and the pulley enters or exits from the meshing state, so that the air at the spout causes the air to compress or dilate, thereby causing air noise.
(1) The wider the width of the silencing zone in the circumferential direction of the timing pulley, the longer the route of the air flow, and the greater the pressure change of the gas, and the greater the noise. Therefore, it is desirable that the width of the timing pulley and the belt be as narrow as possible, but the width of the timing belt has an approximately proportional relationship with the transmitted power. In order to achieve the designed power, the pulley and the belt must have a certain width. In order to overcome this inconsistency, it is possible to slot the pulley circumferentially so that air can be smoothly discharged through the trough, thereby reducing noise. Experiments show that with this method, the noise can be reduced by 3 - 5dB. Slotted as shown in Figure 2.
(2) Synchronous pulley radial opening silencer If you want to further reduce the aerodynamic noise of the timing belt transmission, you can also use the synchronous pulley radial open silencing groove, slotting schematic diagram shown in Figure 3, slotting should pay attention to: 1 Grooves cannot be opened very deep or wide, or they will affect transmission power. The distribution of the two slots should be uniform to avoid breaking the balance of the pulley. 3 Slots must be sharpened to eliminate sharp cuts and burrs to avoid damage to the toothed belt.
3. Conclusion After the above processing, the machine noise will be greatly improved, and the maximum speed of the spindle synchronous belt drive can be increased from 6000r/min to 8000r/min or more.
Article Source: http://www. . Com
Controlling noise mainly starts from two aspects: First, think of methods from sound sources, that is, eliminate or reduce the intensity of sound sources. This is the fundamental method to control noise, and is the focus of this article; the second is to absorb the noise from the transmission route. Sound, sound insulation and other measures to weaken or shield the spread of noise. There are two main reasons for analyzing the noise source of the timing belt drive: on the one hand, due to the excitation of the unbalanced centrifugal force when the two pulleys are rotating, and on the other hand, the disturbance of the gas is caused when the belt and the pulley are meshed. Aerodynamic noise is generated. The main factors that cause noise in these two areas are listed below.
1. Main factors causing rotation imbalance (1) The shape tolerance and position tolerance of the pulley itself, including the tooth-tooth tolerance, tooth thickness tolerance and axial and radial runout of the pulley. The higher the manufacturing precision of the belt and the pulley, the smaller the impact at the time of meshing, and the higher the accuracy of the timing belt transmission, the lower the noise must be. Since both the timing belt and the pulley are manufactured by professional manufacturers, the accuracy of manufacturing can be effectively controlled, which will not be described here.
Parallelism of the two pulley shafts: Under normal circumstances, as the error of parallelism increases, the sound pressure level gradually increases. Therefore, the parallelism of the installation must be ensured when the spindle axis and the motor axis are installed. The parallelism of the two axes must be limited to (0.003 - 0.005)c (c is the center distance of the two pulley shafts).
(2) Rotation accuracy of the two pulley shafts Since both pulleys need to be rotated at a high speed and the rotation speed is higher than 6000 r/min, the unbalanced centrifugal force at the time of high speed rotation will cause tremor of the spindle and the motor shaft if no dynamic balance is performed. This in turn stimulates strong noise. For most manufacturers, only the spindle (including the pulley) has been dynamically balanced during manufacture and assembly. The motor shaft must also be balanced dynamically. The pulley is mounted on the motor shaft and the entire rotary axis is measured using a line dynamic balancer. The test was conducted and the material balance method was used to perform dynamic balancing (drilling on the pulley) to require the final dynamic balance accuracy level to reach G2.5. After this treatment, the vibration and noise of the drive can be reduced to different extents, and it is also very beneficial to increase the service life of the timing belt and the main shaft.
(3) The pre-tensioning force of the timing belt is different from that of the flat belt and the v-belt. The timing belt relies on meshing to transmit power, so it does not require much pre-tension. Excessive tension will seriously affect the service life of the belt. Serious noise. Under the effect of starting and impact torque, too small tension may cause the timing belt to skip and cause root fracture. How to choose the proper tension The more accurate method is to use the ultrasonic tension tester. If there is no tester, a simple set of tooling can also be made and measured as follows: As shown in Figure 1, one side of the timing belt is close to two belts. At the center of the wheel, a test force is applied, and the belt is bent inward to produce a deformation d. If d=S/64 (s is the single measurement length of the belt, unit: mm), the tension of the belt is considered to be appropriate. . Otherwise, the belt tension measurement diagram of Figure 1 adjusts the tension of the belt until it is suitable. The values ​​vary depending on the type and bandwidth of the tape. Specific information can be found. For example, for 40mm wide 8YU (8M) timing belts, d takes 39N. Experiments have shown that proper tensioning of belts can significantly reduce high-frequency noise, which is often referred to as "whistling sound."
Pulley tension measurement diagram 2. Control of aerodynamic noise In the case of high-speed rotation of the pulley, the high frequency of the meshing teeth of the belt and the pulley enters or exits from the meshing state, so that the air at the spout causes the air to compress or dilate, thereby causing air noise.
(1) The wider the width of the silencing zone in the circumferential direction of the timing pulley, the longer the route of the air flow, and the greater the pressure change of the gas, and the greater the noise. Therefore, it is desirable that the width of the timing pulley and the belt be as narrow as possible, but the width of the timing belt has an approximately proportional relationship with the transmitted power. In order to achieve the designed power, the pulley and the belt must have a certain width. In order to overcome this inconsistency, it is possible to slot the pulley circumferentially so that air can be smoothly discharged through the trough, thereby reducing noise. Experiments show that with this method, the noise can be reduced by 3 - 5dB. Slotted as shown in Figure 2.
(2) Synchronous pulley radial opening silencer If you want to further reduce the aerodynamic noise of the timing belt transmission, you can also use the synchronous pulley radial open silencing groove, slotting schematic diagram shown in Figure 3, slotting should pay attention to: 1 Grooves cannot be opened very deep or wide, or they will affect transmission power. The distribution of the two slots should be uniform to avoid breaking the balance of the pulley. 3 Slots must be sharpened to eliminate sharp cuts and burrs to avoid damage to the toothed belt.
3. Conclusion After the above processing, the machine noise will be greatly improved, and the maximum speed of the spindle synchronous belt drive can be increased from 6000r/min to 8000r/min or more.
Article Source: http://www. . Com
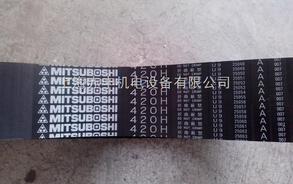
Chain Lifting Platform,Lifting Platform Chain Machine,Stage Lifting Tower Masts,Stage Lifting Tower Mast
TIANHEMAST , https://www.robomasts.com