Figure 1 Scanning point distribution for bending and torsional vibration measurements
Specific measurement situation
In order to avoid external vibrations in the experimental analysis, a large-quality steel measuring platform was used. First, the spindle and center of gravity of the single-edged drill must be calculated so that the longitudinal vibration direction of the drill can be directly aligned with the center of gravity of the drill and the lateral direction of the spindles on both sides. For vibration in the longitudinal direction of the drill bit, the vibrator and the single-edged drill bit are tensioned against each other on a tiger table or a jig with a liner and a clamp . The free end of the drill has a hardened vibrating apex with a Piezo load cell and an aluminum adapter. These devices can be connected to the vibrator under the action of tension. The controller transmits an sinusoidal signal and a specific frequency band through an amplifier to a vibrator that vibrates at the other end to the single-edged drill bit. The load cell feeds the force signal back to the controller through a load-carrying amplifier, and the controller calculates the modal parameters through the frequency-dependent stroke change signal transmitted by the laser scanning vibrometer.
Figure 2 Frequency of flexibility in the first main axis direction (34)
Fig. 2 shows the flexibility frequency range of the φ11.76mm single-edged deep-hole drill bit in the first main shaft direction (34), and the curve conforms to the characteristics of the conventional three-position vibrator. This experimental approach is appropriate because the three-position distribution involves drill bits, drill rods and tensioning sleeves for single-edged drills. The 880Hz self-owned mode is easy to recognize, which is a bending vibration; and the other own mode is 2000Hz torsional vibration. The third typical self mode is still bending vibration with a frequency of 3300 Hz. For ease of comparison, the flexural frequency range of the single-edged drill bit when the drill shown in Figure 3 is subjected to vibration in the feed direction. The first measured mode is 580 Hz and the second own mode is 850 Hz. These are all bending vibrations. An atypical vibration amplitude observed in the direction of the first major axis is the first torsional vibration of 2000 Hz. Typical examples are the 2600Hz, 3300Hz, and 3860Hz modes, which are bent from vibration.
Previous Next
Rolling Mill Bearing for blanking machine .
Rolling mill bearings are the bearings used on the roll necks and rollers of metallurgical, mining and other rolling mill stands. Cylindrical roller bearings are often used to withstand radial loads, deep groove ball bearings or angular contact ball bearings, or radial design or thrust design Tapered Roller Bearings to withstand axial loads. Most of them are lubricated and cooled by means of oil-air lubrication or oil mist lubrication.
Rolling Mill Main Application:
Cold rolling mill, Hot rolling mill, Blanking machine
Roll neck and drum for metallurgy, mining and other rolling mill stands
Model No.
|
ID (mm)
|
OD (mm)
|
W (mm)
|
Weight (kg)
|
FC2028104
|
100
|
140
|
104
|
5.2
|
FC202870
|
100
|
140
|
70
|
3.7
|
381040X2
|
200
|
310
|
200
|
55.6
|
380641
|
205
|
320
|
205
|
55.4
|
382040
|
200
|
310
|
275
|
75.1
|
FC2030106
|
100
|
150
|
106
|
6.8
|
FC202970
|
100
|
145
|
70
|
4.1
|
FC202880
|
100
|
140
|
80
|
4
|
FC202870M
|
100
|
140
|
70
|
3.7
|
FC202870/P6
|
100
|
140
|
70
|
3.7
|
FC2028104M
|
100
|
140
|
104
|
0
|
FC2028104/P6
|
100
|
140
|
104
|
5.2
|
FC2028104/P5
|
100
|
140
|
104
|
5.2
|
FC182870
|
90
|
140
|
70
|
4.4
|
381050X2/YA
|
250
|
460
|
270
|
192
|
382052X2
|
260
|
400
|
255
|
117
|
20FC1570
|
100
|
145
|
70
|
3.8
|
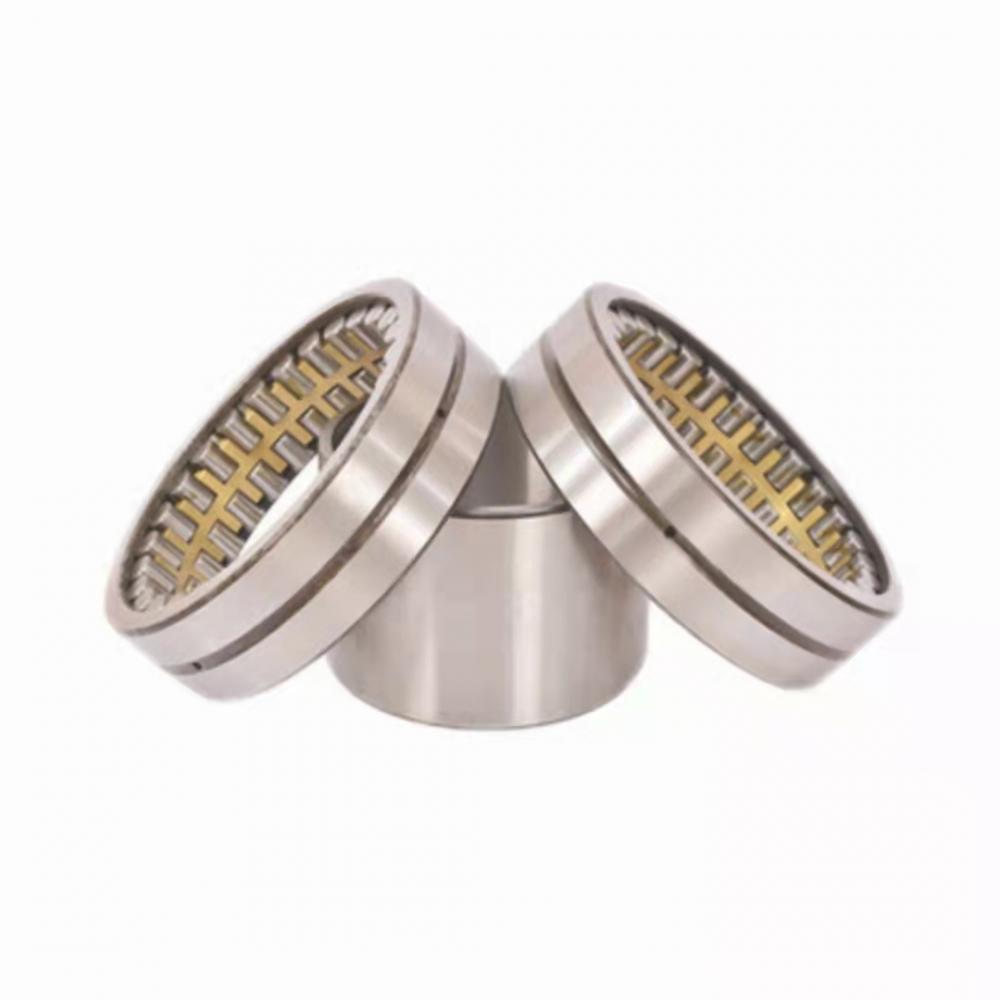
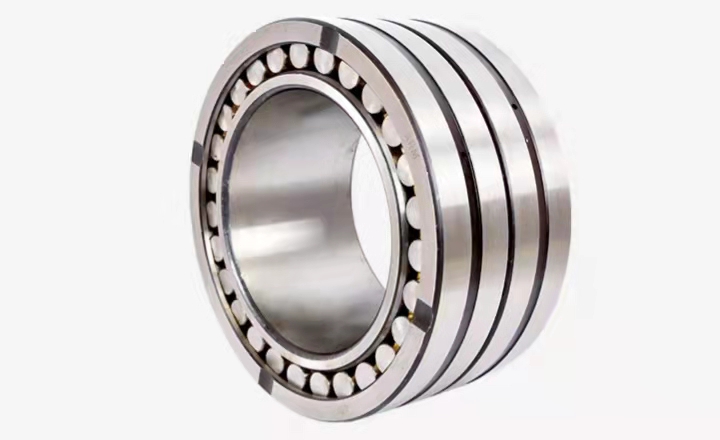
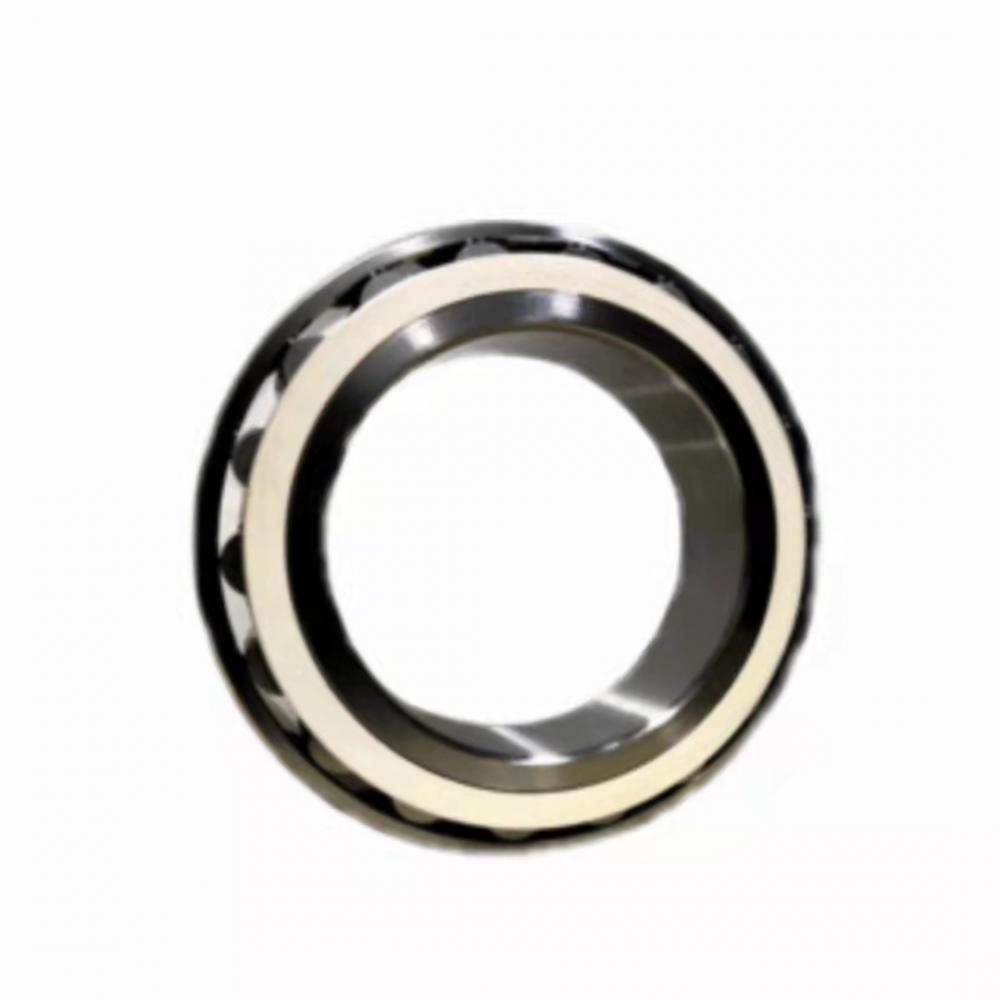
Fcd Rolling Mill Bearing,Fcd Rolling Bearing,Bearing For Steel,Bearing For Steel Mill
Shijiazhuang Longshu Mechanical & Electrical Equipment Trading Co., Ltd. , https://www.longsbearing.com