As global vehicle production grows and demand for high-performance, low-energy engines increases, more and more engines use turbochargers, and the production of impellers is changing. The tradition of machining aluminum alloy casings by impellers The way is gradually replaced by milling. The overall structure of the impeller is complex, and the blade is twisted. When the CNC machine tool is processed, it is easy to have interference collision. Especially when the surrounding blade is fed, since the tool passes through the blade flow path, it is easy to collide with the adjacent blade, especially to the blade. When the roots. The closed impeller can only be processed by two clamping methods, and the interference collision is not as serious as the open integral impeller. Therefore, in the tool path calculation, the smoothing of the tool bar vector generation is the key and difficult point to achieve non-interference efficient machining.
For the principle of turbocharger, please refer to the principle of turbocharger.
Impeller machining tool path
Five-axis cutting has special process requirements than traditional cutting. In addition to five-axis cutting machines and cutting tools , proper CAM programming software is required . An excellent five-axis machining CAM programming system should have high calculation speed, strong interpolation function, full automatic inspection and processing capability, automatic tool holder and fixture interference check, feed rate optimization processing function, tool Track editing optimization function and machining residual analysis function. When programming NC, we must first pay attention to the safety and effectiveness of the machining method. Secondly, we must do everything possible to ensure that the tool path is smooth and stable, which will directly affect the processing quality and the service life of the machine tool spindle and Other parts. Third, we should try to make the tool load uniform. This will directly affect the life of the tool . In addition, the overall impeller blades are thin, have large distortion, and the probability of machining interference is high, which is the main factor affecting the quality of five-axis programming. Even if the above problems are solved well, another important problem is to control the sudden change of the tool bar during the movement, because the sudden change of the tool bar will directly affect the sudden increase of the coordinate direction of the machine tool during the machining process, even Exceeds the machine 's motion limit.
The impeller is a typical free-form surface part. If the traditional CAM machining strategy is adopted, it is necessary to repeatedly test different machining orientations and spend a lot of time to adjust. It is time-consuming and difficult to guarantee accuracy. hyperMILL provides for both open and closed impeller machining. The professional processing module allows even users with less processing experience to easily set up a NC program for parts machining that is difficult to complete with conventional programming strategies.
Tool selection
In order to improve the processing efficiency, a large-diameter ball-end milling cutter is used as much as possible in the roughing of the flow path and the semi-finishing of the flow path, but the diameter of the tool must be smaller than the minimum distance between the two blades. In the process of blade finishing, the large diameter ball nose cutter should be selected as much as possible under the premise of ensuring no cutting, that is, the maximum radius of the tool is larger than the maximum rounding radius of the runner and the blade. When the intersection of the flow path and the adjacent blade is rooted, the selected tool radius is smaller than the minimum rounding radius of the flow path and the blade intersection. The tools selected this time are a 25mm diameter round nose knife, a 12mm diameter ball cutter and a 8mm diameter tapered ball cutter (see Figure 2? Figure 4).
Figure 2 round nose knife
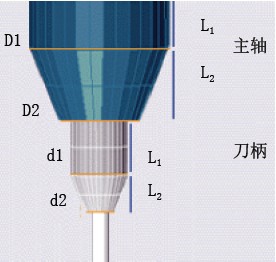
Figure 3 ball knife
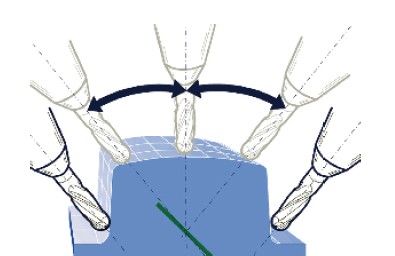
Figure 4 Taper ball cutter

Figure 5 spindle positioning
1. nut 2. washer 3. mandrel
kaiping aida sanitary ware technology co.,ltd , https://www.kpfaucets.com